Машиностроение
и металлообработка
Семейство цифровых продуктов для эффективного управления производственным оборудованием и контроля технологических процессов в дискретной отрасли
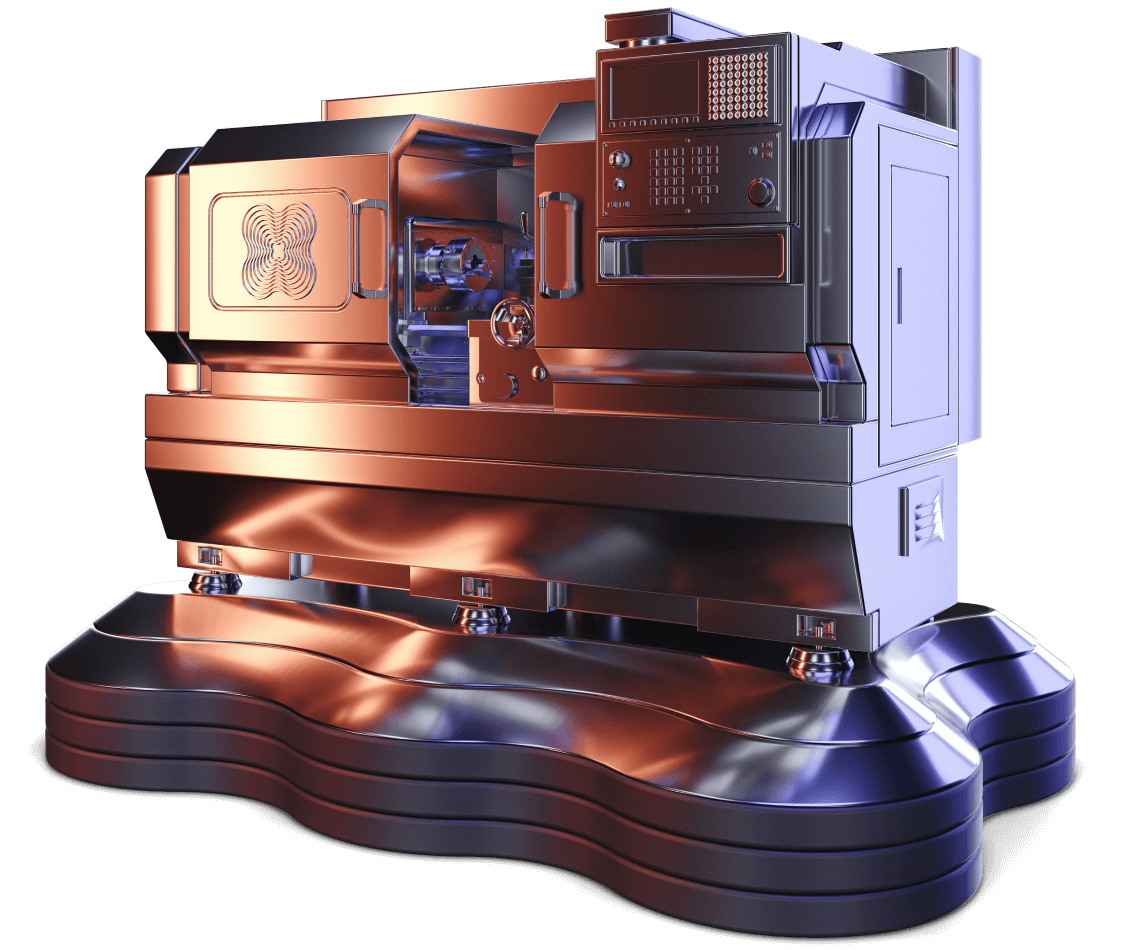
Новости
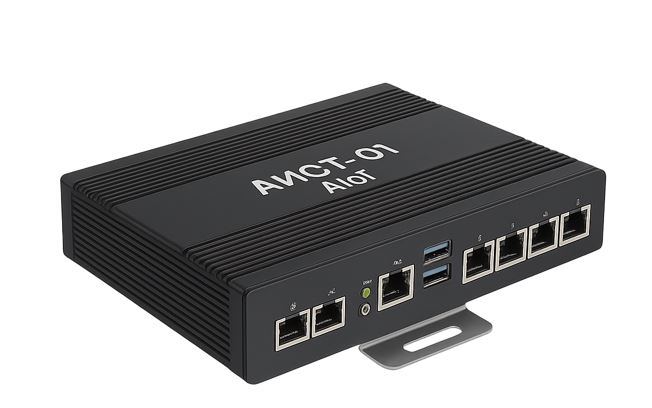
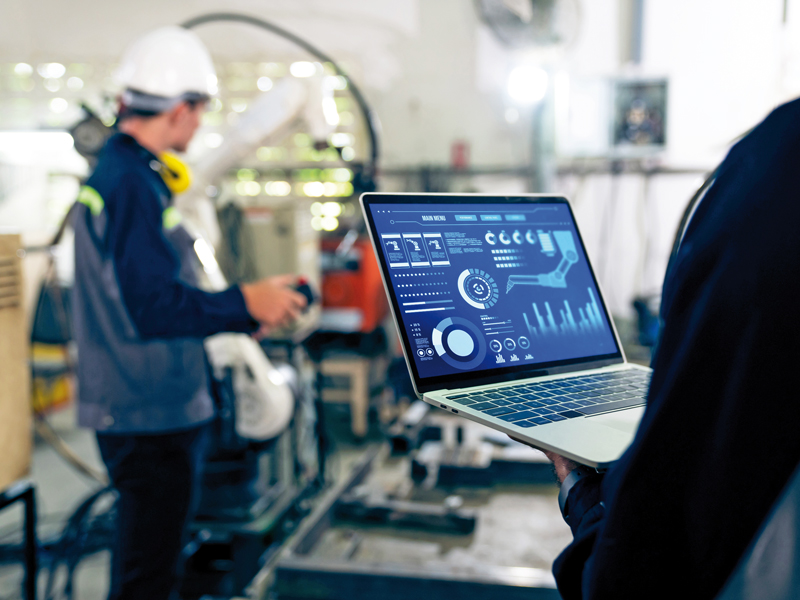
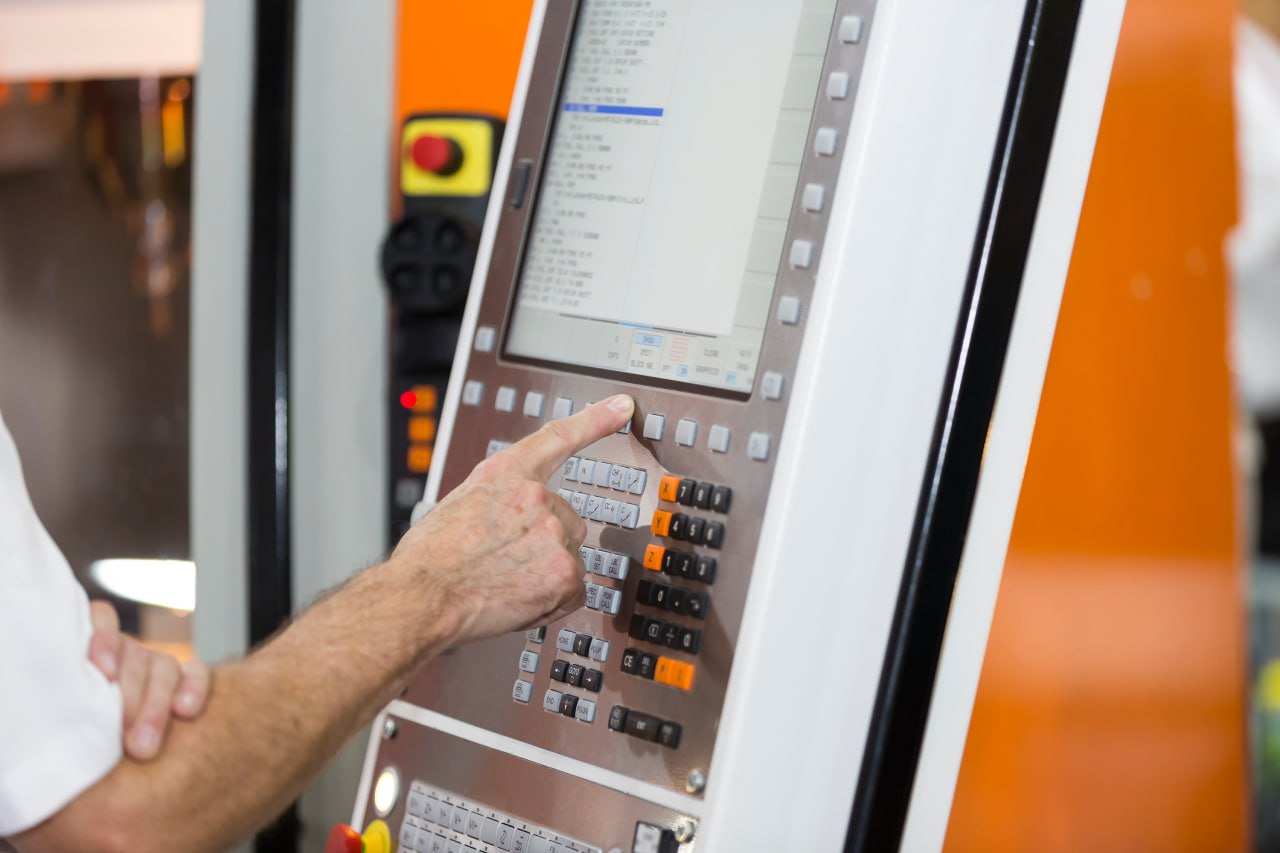
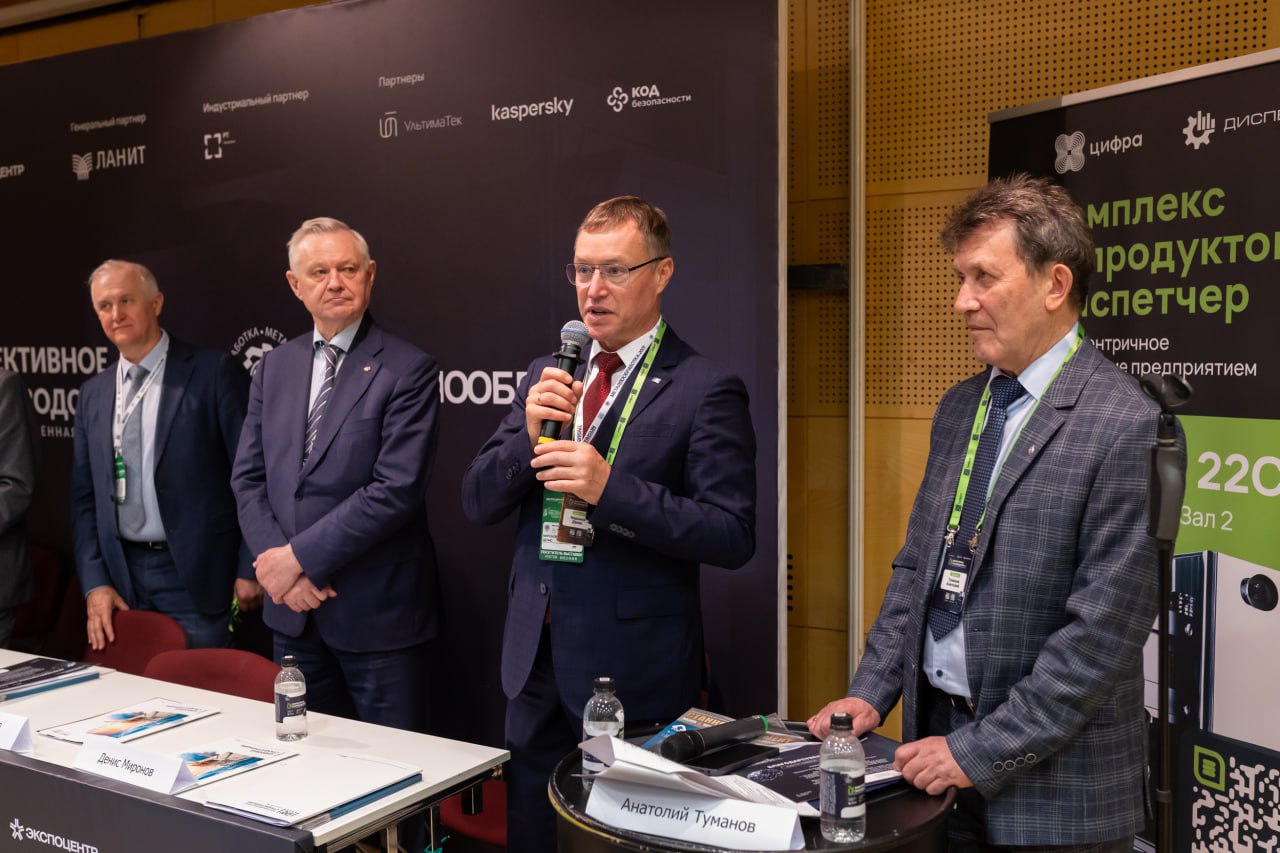
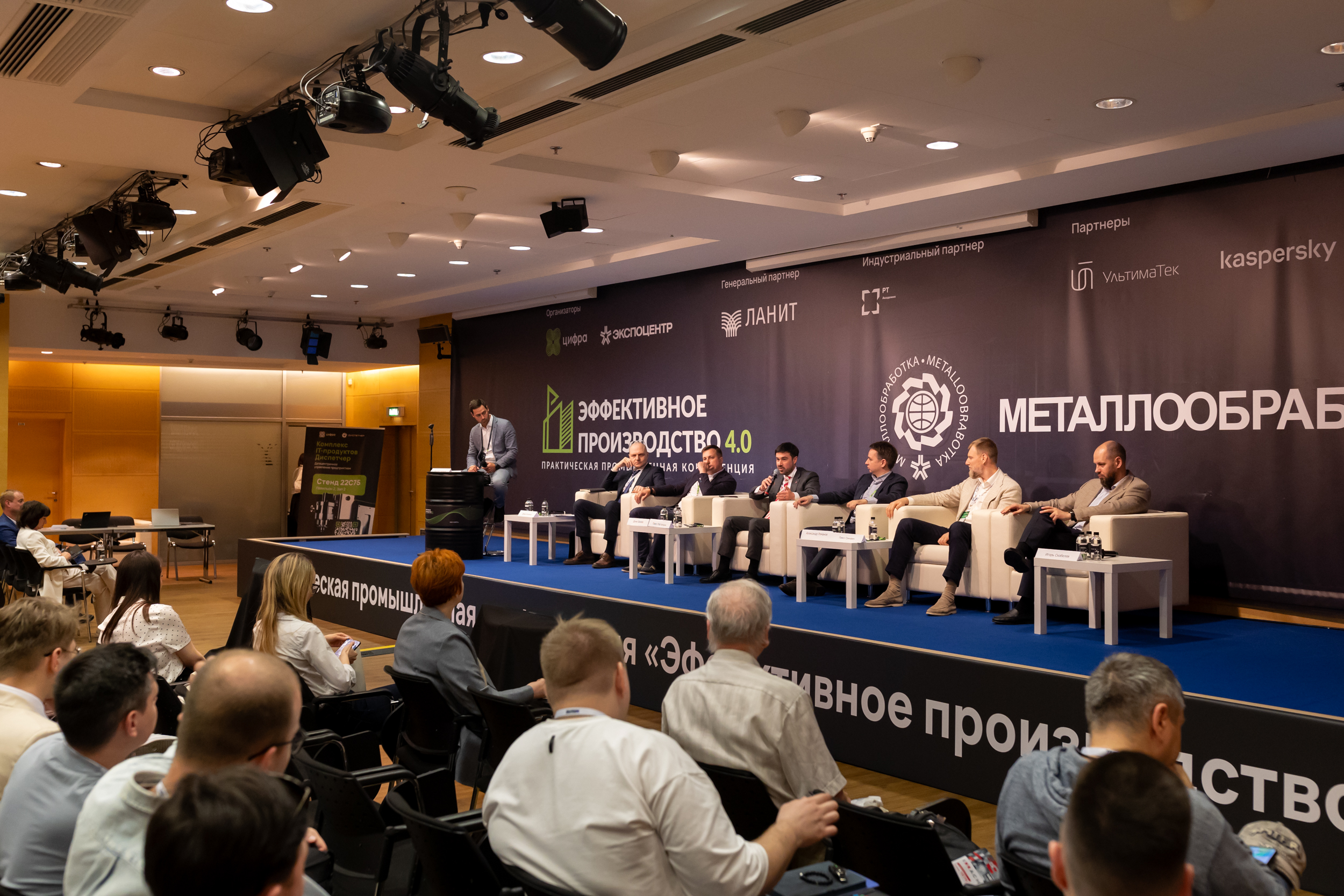
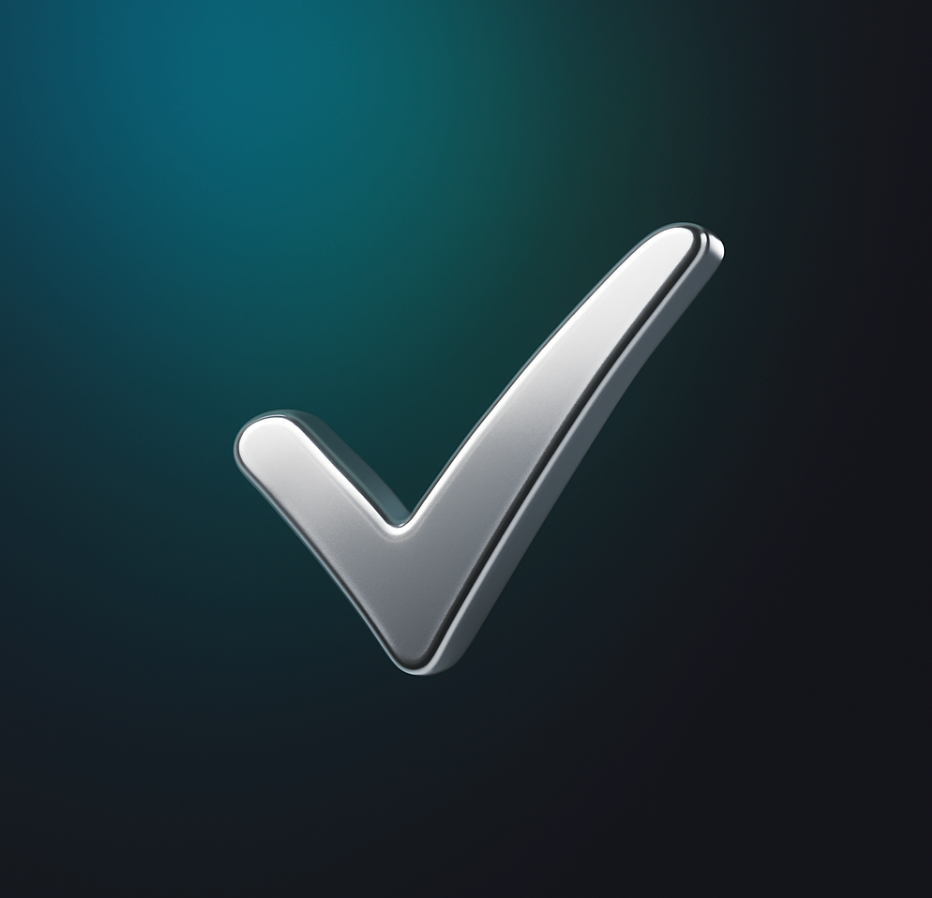
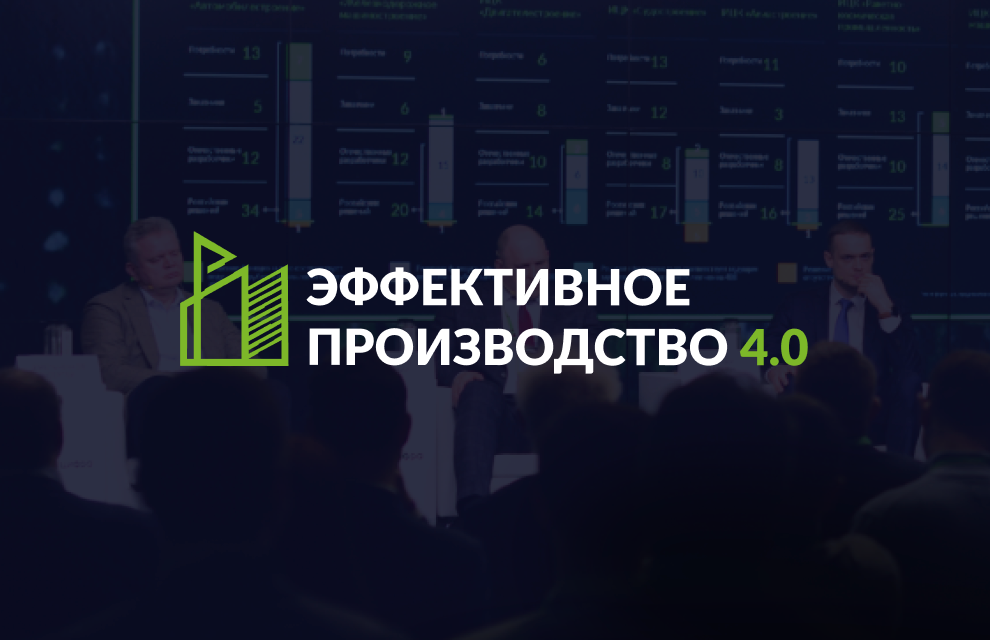
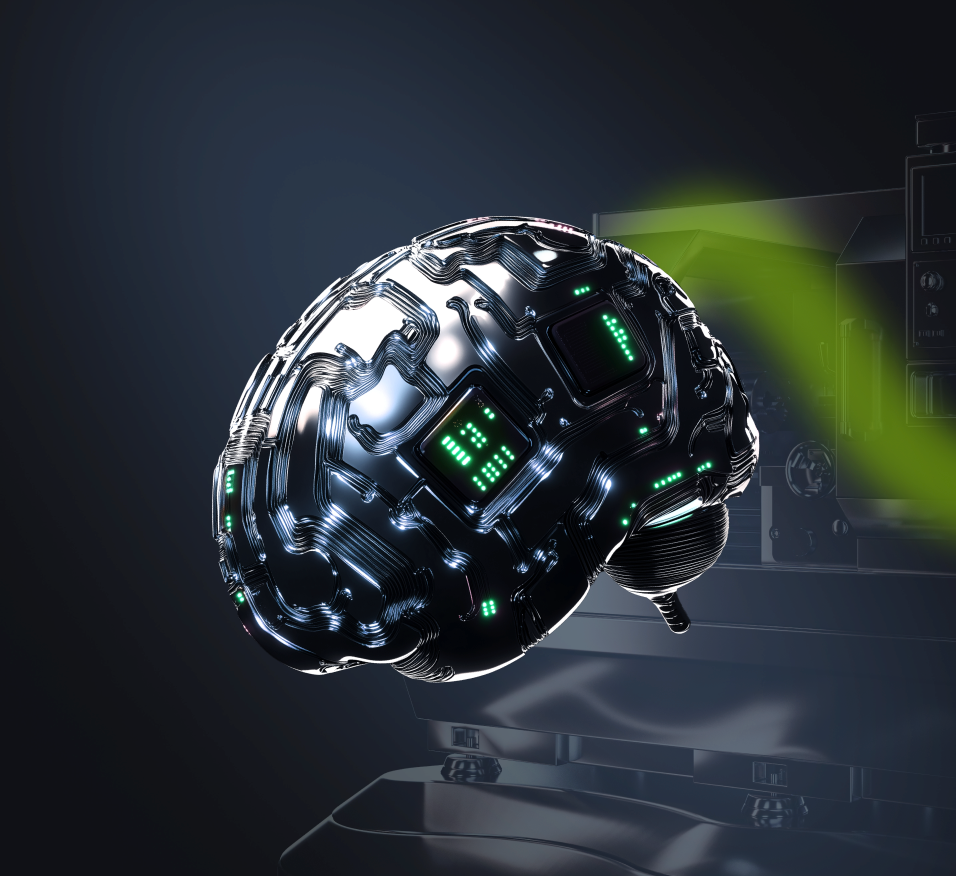
О задачах цифровизации
в машиностроении и металлообработке
- Наращивание объемов
и темпов производства без потери качества для выполнения государственных контрактов - Развитие функционала
и повышение надежности выпускаемых изделий - Запуск и отладка выпуска новой инновационной продукции
- Увеличение
производительности труда - Совершенствование практик
охраны труда и промышленной безопасности - Выполнение требований
по информационной безопасности и импортонезависимости производств
для дальнейшего технологического развития, предприятиям требуются цифровые системы, помогающие:
Делать производство прозрачным и точнее оценивать резервы мощностей, вовремя замечать отклонения от сроков выполнения заказов
Поддерживать стабильную работу производственного оборудования, следить за режимами его использования и предотвращать поломки, влекущие остановы производства
Быстро и качественно аккумулировать производственную информацию для поддержки управленческих решений, направленных на наращивание пропускной способности производства
Обеспечивать своевременную закупку оборудования и запчастей, расходных материалов, комплектующих для стабильной работы производства в условиях усложнения закупочных циклов и ограниченного доступа к ряду зарубежных продуктов
Эффективно планировать производство и контролировать материальные потоки и ресурсы, управлять оборудованием и персоналом и формировать производственную отчетность для оперативного управления производством
Контролировать качество выпускаемой продукции на должном уровне эффективности и достоверности
Эффекты наших клиентов от внедрения
цифровых систем
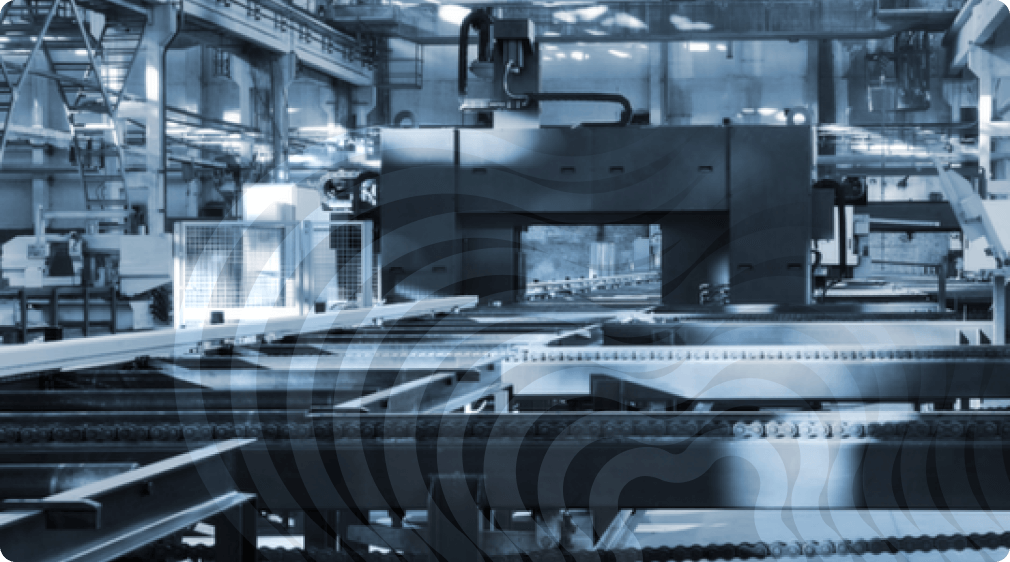
- Рост объема выпуска продукции
без наращивания мощностей - Ускорение выполнения
производственных заказов - Повышение прослеживаемости
- Сокращение простоев и аварий
- Сокращение затрат на производство
Продукты «Цифры»
для дискретных производств
флагманская разработка ГК «Цифра» для цифровизации и повышения эффективности предприятий машиностроения и металлообработки. В его основе лежит IoT-технология, обеспечивающая автоматизированный сбор и обработку промышленных данных в режиме реального времени.
- 01Может применяться на разных стадиях цифровой зрелости предприятий
- 02Способен стать основой для цифровой трансформации производств дискретного типа
- 03Отвечает всем требованиям информационной безопасности и защиты КИИ
- 04Не содержит импортозависимых компонентов и микросервисов
- 05Сертифицирован ФСТЭК
Комплекс «Цифра. Диспетчер» состоит из самостоятельных продуктов:
- Оперативный контроль работы станков
- Учет и классификация простоев
- Оповещение о фактах и причинах нештатных ситуаций
- Расчет ключевых показателей эффективности и автоматическое формирование отчетности
- Контроль производственной дисциплины
- Формирование оптимального плана производства
- Контроль выполнения планов в режиме реального времени
- Документирование и управление производственными заказами
- Отслеживание технологий производства
- Учет изделий, материалов, инструментов, оснастки, расходников и комплектующих
- Контроль технического состояния производственного оборудования, в том числе на основе вибромониторинга
- Ведение нормативно-справочной информации по ТОиР
- Автоматизированное планирование ТОиР с учетом данных о наработке и состоянии оборудования
- Контроль выполнения ремонтных работ
- Учет запчастей и расходных материалов
- Агрегация и анализ данных с производственных площадок, сравнение показателей эффективности
- BI с продвинутой аналитикой для топ-менеджмента
- Анализ пропускной способности производства
- Сопровождение процессов внутрихолдинговой кооперации
- Прогнозирование загрузки с учетом задач холдинга
Обсудим ваш проект?
Зададим вопросы, уточним задачу и предложим лучший набор решений, опираясь на опыт десятков проектов с главными предприятиями страны.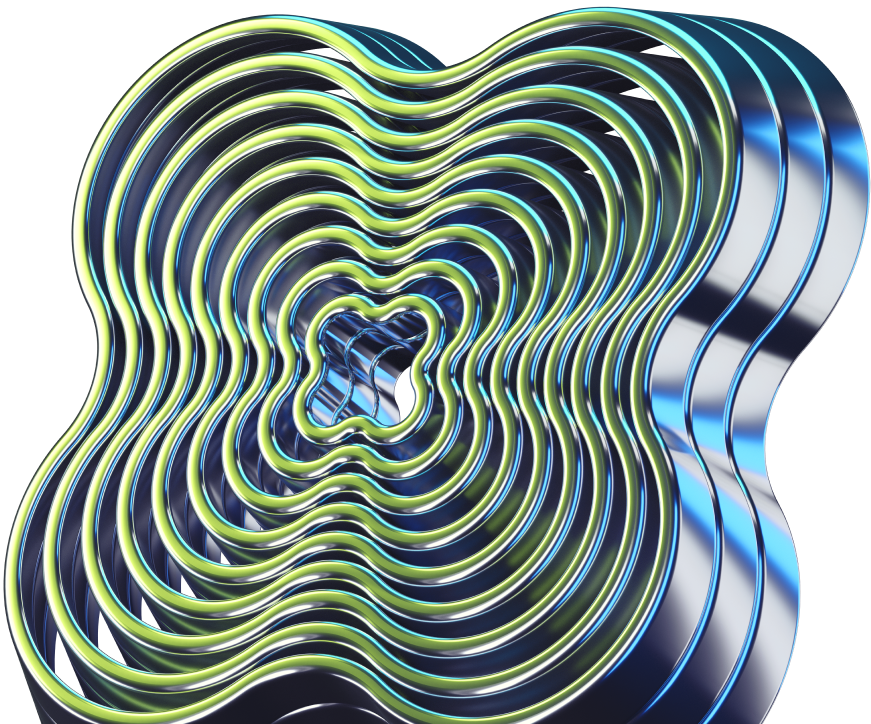
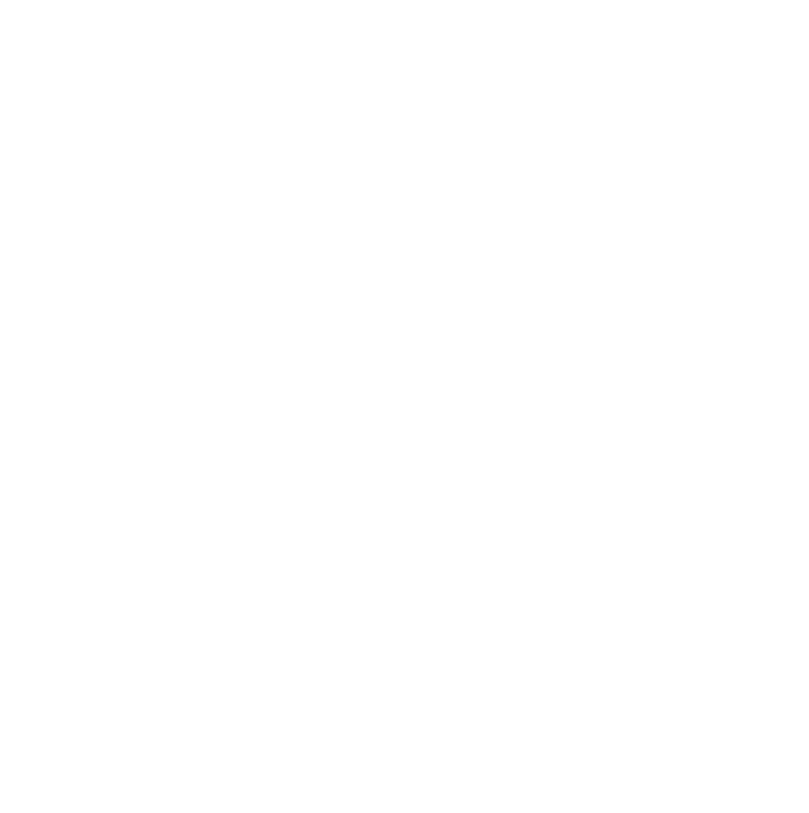
«Цифра»
в машиностроении и металлообработке
- 20+лет опыта в машиностроении и металлообработке
- 150+сотрудников в дивизионе «Машиностроение и металлообработка»
- 500+цифровизированных предприятий
- 16 000+подключенных единиц оборудования
- 600 млрд ₽выручка четырёх промышленных холдингов, включивших «Цифра. Диспетчер» в стратегию цифрового развития
Цифра. Академия
Мы верим, что эффективная цифровая трансформация возможна только при наличии квалифицированного и мотивированного персонала и постоянного контакта с экспертным сообществом. Для этого мы запустили и поддерживаем проекты, направленные на развитие цифровых компетенций промышленников и организацию обмена лучшими практиками цифровизации в машиностроении и металлообработке.
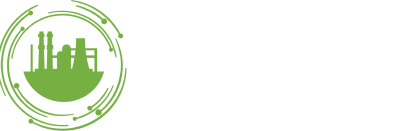
Серия онлайн-курсов, созданных в партнерстве с ведущими вендорами, интеграторами, ИТ-разработчиками и промышленными предприятиями, дает единое понимание экосистемы цифровых технологий и подходов к цифровизации производства дискретного типа. На конкретных примерах внедрения, на ошибках и успехах мы разбираем ключевые шаги и «узкие места» при реализации цифровой стратегии.
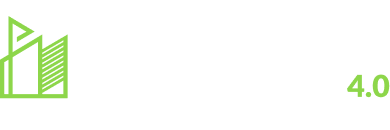
Ежегодное мероприятие ГК «Цифра» уже 8 лет служит местом для дискуссий и обмена опытом для крупнейших промышленных предприятий и поставщиков цифровых решений. В 2024 году конференция вошла в деловую программу международной выставки «Металлообработка» и стала центральной площадкой по вопросам цифровизации машиностроительных и металлообрабатывающих производств в России.
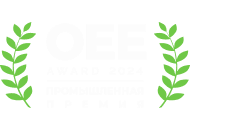
Ежегодная премия за эффективные проекты цифровизации способствует поиску и популяризации лучших цифровых практик и инновационных решений для повышения эффективности и безопасности производства в машиностроении и металлообработке.
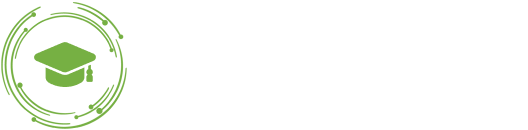
Учебный центр ГК «Цифра» на регулярной основе проводит обучение собственных специалистов, а также партнеров и клиентов по внедрению и использованию комплекса продуктов «Цифра. Диспетчер» и лучшим практикам цифровизации машиностроительных и металлообрабатывающих производств.
Дивизион «Машиностроение и металлообработка»
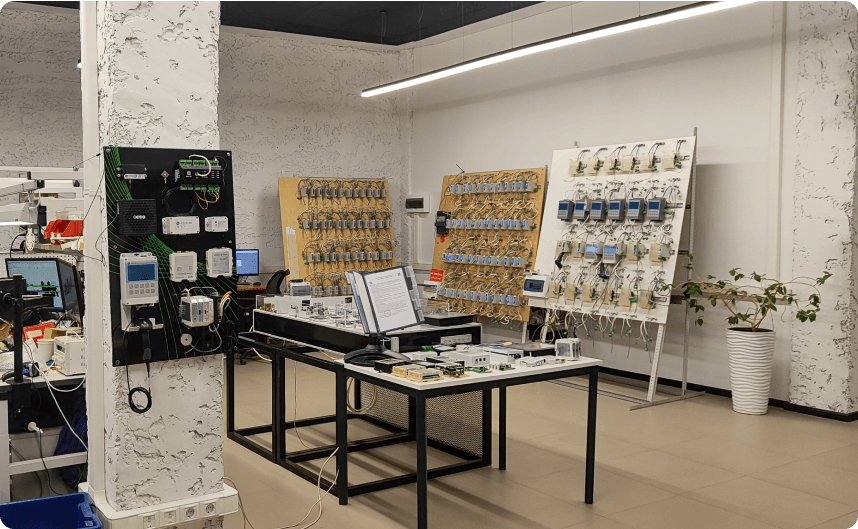
Над созданием продуктов для производств дискретного типа в группе компаний «Цифра» работает дивизион «Машиностроение и металлообработка». Это команда профессионалов с богатым производственным опытом и сильными компетенциями в сфере инновационных технологий. Центр разработки дивизиона базируется в Смоленске, а головной офис — в Москве. У дивизиона также есть собственный сборочный цех, отвечающий за аппаратное обеспечение проектов цифровизации и позволяющий обеспечить их соответствие требованиям по информационной безопасности и импортонезависимости.
История дивизиона
Команда энтузиастов, работавших на крупных машиностроительных заводах Смоленска, создает инновационный центр «Станкосервис» для разработки промышленных цифровых решений
«Станкосервис» становится резидентом Сколково и начинает развивать систему мониторинга промышленного оборудования «Цифра. Диспетчер»
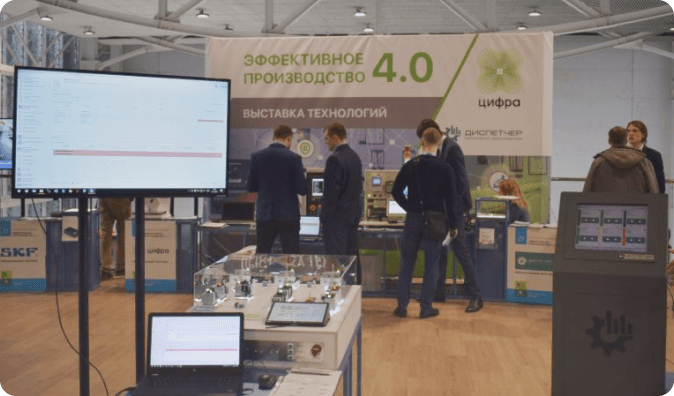
Запуск собственной отраслевой конференции «Эффективное производство 4.0»
«Станкосервис» входит в состав группы компаний «Цифра» как дивизион «Машиностроение и металлообработка»
Выпуск модуля «Цифра. Диспетчер ТОиР»
Запуск совместно с Академией Ростеха онлайн-практикума «Цифровое производство» для инженеров и руководителей промышленных компаний
Выпуск модуля «Цифра. Диспетчер MES»
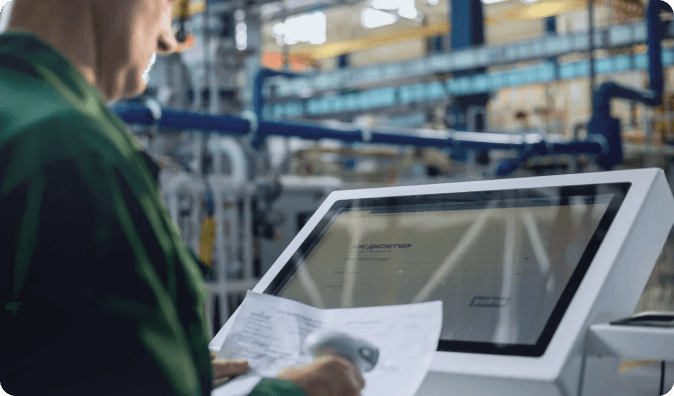
«Цифра. Диспетчер» занимает более 70% рынка систем промышленного мониторинга России
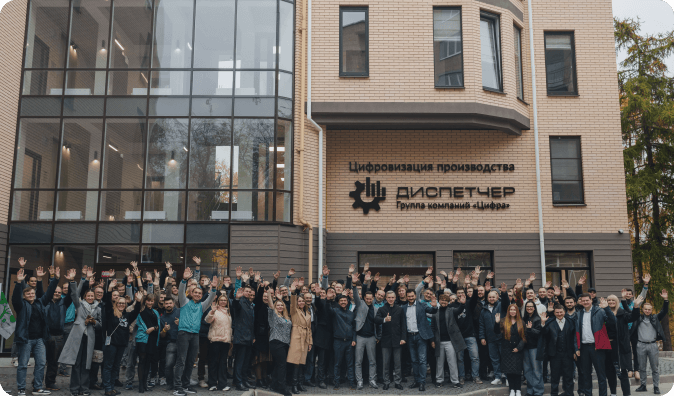
Дивизион «Машиностроение и металлообработка» открывает отраслевой центр компетенций по цифровизации промышленности в Смоленске
Мы рядом с крупнейшими
индустриальными центрами страны
Центр разработки продуктов находится в Смоленске, головной офис — в Москве.
У нас развита сеть партнеров-интеграторов по всей России и ближнему зарубежью. Мы всегда на связи с крупнейшими машиностроительными и металлообрабатывающими предприятиями.
- Москва
- Казань
- Екатеринбург
- Минск
- Кемерово
- Нижний Новгород
- Краснодар
- Курск
- Архангельск
- Смоленск
- Снежинск
- Ульяновск
Награды
Контакты для прессы
Взаимодействие с органами гос.власти и партнёрами
Техническая поддержка
Контакты для прессы
Взаимодействие с органами гос.власти и партнёрами
Техническая поддержка
Отрасли
Контакты для прессы
Взаимодействие с органами гос.власти и партнёрами
Техническая поддержка
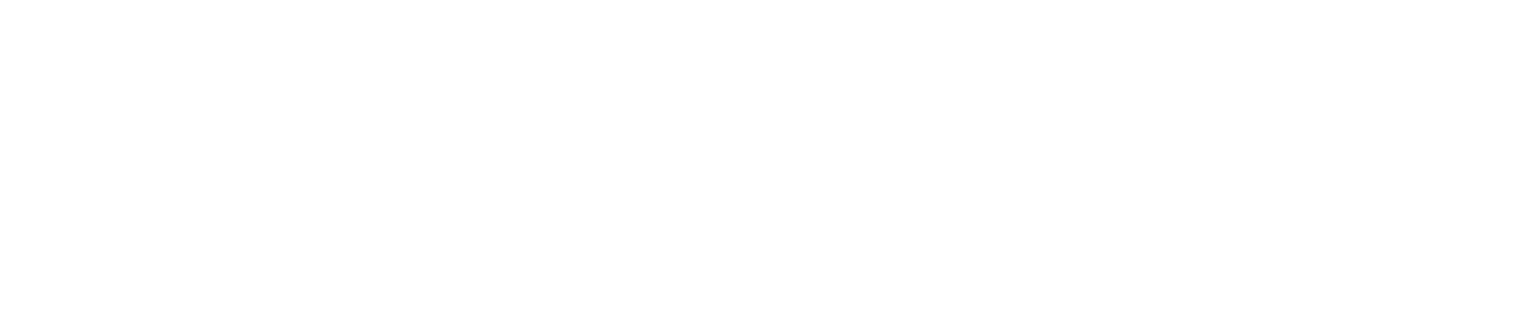